The top ramen recall has become a significant topic of concern for many consumers around the world. With instant noodles being a staple in many households due to their convenience and affordability, a recall can spark considerable alarm. This article aims to delve into the intricate details of the top ramen recall, shedding light on its causes, effects, and the measures taken to address the issue.
In recent years, food recalls have become increasingly common due to heightened safety standards and better detection methods. The top ramen recall is a part of this larger trend, as companies strive to ensure the safety and well-being of their consumers. By understanding the reasons behind such recalls, consumers can make informed decisions about their food choices and trust the brands they support.
The purpose of this article is to provide a comprehensive overview of the top ramen recall, exploring its origins, the response from the manufacturers, and the implications for consumers. Through a series of detailed headings and subheadings, readers will gain a deeper understanding of the recall process and the steps taken to prevent future occurrences. With a focus on factual information and expert insights, this article will offer a balanced perspective on the top ramen recall.
Table of Contents
- What Caused the Top Ramen Recall?
- How Did the Manufacturer Respond?
- Impact on Consumers
- Safety Standards in the Food Industry
- Preventive Measures and Solutions
- What Are the Lessons Learned?
- Consumer Awareness and Education
- Role of Regulatory Bodies
- Economic Impact of the Recall
- Global Perspective on Food Recalls
- What Are the Future Prospects?
- Consumer Feedback and Its Significance
- How Does It Affect Brand Loyalty?
- Role of Social Media in Recalls
- Conclusion
What Caused the Top Ramen Recall?
The top ramen recall was initiated due to the detection of potential health risks associated with certain batches of the product. These risks could stem from various factors, such as contamination, mislabeling, or the presence of undeclared allergens. The exact cause of the recall is often determined through rigorous investigation and testing processes conducted by both the manufacturer and regulatory bodies.
Contamination could occur at any stage of production, from raw material sourcing to packaging. Common contaminants include bacteria, foreign objects, or chemical residues. Mislabeling, on the other hand, may involve incorrect ingredient lists or nutritional information, leading to potential health risks for certain consumers, particularly those with allergies or dietary restrictions.
Understanding the Recall Process
The recall process is a structured procedure that involves several stages. Initially, the manufacturer may receive reports of issues from consumers or regulatory authorities. This triggers an internal investigation to ascertain the validity and scope of the problem. Once confirmed, the company publicly announces the recall, providing details about the affected products and instructions for consumers.
During this process, communication is crucial. Manufacturers must work closely with retailers and regulatory agencies to ensure that the recalled products are removed from shelves and that consumers are adequately informed. This transparency helps maintain consumer trust and mitigates potential harm.
How Did the Manufacturer Respond?
In response to the top ramen recall, the manufacturer took immediate action to address the concerns and ensure consumer safety. One of the primary steps involved halting the production and distribution of the affected batches. This prompt action is essential to prevent further exposure to potentially harmful products.
The company also issued public statements and press releases to inform consumers about the recall. These communications typically include details about the specific products affected, the nature of the risk, and instructions for consumers on how to proceed. This might involve returning the products for a refund or exchanging them for a safe alternative.
Collaboration with Regulatory Bodies
Manufacturers often collaborate with regulatory bodies during a recall to ensure compliance with safety standards and regulations. This partnership is vital for conducting a thorough investigation and determining the root cause of the issue. Regulatory bodies may also provide guidance on best practices for managing the recall and preventing future incidents.
Through this collaborative effort, manufacturers can implement corrective measures and improve their production processes to enhance product safety. This not only addresses the immediate issue but also contributes to long-term improvements in food safety standards.
Impact on Consumers
The top ramen recall significantly impacts consumers, particularly those who rely on instant noodles as a quick and affordable meal option. The recall may cause inconvenience and concern, as consumers must identify affected products and navigate the return or exchange process. Additionally, consumers may feel a loss of trust in the brand, questioning the safety and integrity of its products.
For some consumers, particularly those with specific dietary requirements or allergies, the recall poses a serious health risk. In such cases, the recall serves as a crucial reminder of the importance of vigilance and awareness when selecting food products.
Rebuilding Consumer Trust
Rebuilding consumer trust after a recall is a challenging but essential task for manufacturers. Companies must demonstrate transparency and accountability, keeping consumers informed throughout the recall process and beyond. This can be achieved through regular updates, public apologies, and assurance of corrective actions.
Engaging with consumers on social media and other platforms is also an effective strategy for rebuilding trust. By addressing concerns and responding to inquiries promptly, manufacturers can show their commitment to consumer safety and satisfaction.
Safety Standards in the Food Industry
Safety standards in the food industry are stringent and continually evolving to protect consumers from potential health risks. These standards are established by regulatory bodies and industry organizations, outlining guidelines for safe production, handling, and distribution of food products.
Manufacturers must adhere to these standards to ensure their products are safe for consumption. This involves implementing quality control measures, conducting regular inspections, and maintaining detailed records of production processes. Compliance with safety standards is not only a legal obligation but also a critical component of building consumer trust and brand reputation.
The Role of Technology in Ensuring Safety
Advancements in technology have significantly contributed to enhancing food safety standards. From sophisticated testing methods to automated production systems, technology plays a crucial role in identifying and mitigating potential risks. For instance, advanced testing can detect contaminants at lower levels, allowing for earlier intervention and prevention of widespread issues.
Moreover, technology enables better traceability and transparency throughout the supply chain. With the use of data analytics and blockchain, manufacturers can track the journey of raw materials and finished products, ensuring accountability and compliance with safety standards.
Preventive Measures and Solutions
Preventive measures are essential in mitigating the risk of future recalls and ensuring the safety of food products. Manufacturers must prioritize these measures to safeguard consumer health and maintain brand integrity. This involves a proactive approach to identifying potential risks and implementing solutions to address them before they escalate into significant issues.
One of the key preventive measures is the implementation of robust quality control systems. These systems should encompass all stages of production, from sourcing raw materials to packaging and distribution. Regular inspections and audits are crucial in ensuring compliance with safety standards and identifying areas for improvement.
Training and Education for Employees
Training and education for employees are vital components of preventive measures. By equipping employees with the knowledge and skills needed to identify and address potential risks, manufacturers can enhance overall safety and quality. This includes training on hygiene practices, handling procedures, and the use of technology to monitor and control production processes.
Continuous education and awareness programs also help foster a culture of safety within the organization. By prioritizing safety and quality, manufacturers can reduce the likelihood of recalls and build a reputation as a reliable and trustworthy brand.
What Are the Lessons Learned?
The top ramen recall offers valuable lessons for both consumers and manufacturers. For consumers, the recall serves as a reminder of the importance of vigilance and awareness when selecting food products. By staying informed about recalls and understanding the risks associated with certain products, consumers can make better choices and protect their health.
For manufacturers, the recall highlights the need for continuous improvement in safety standards and production processes. It emphasizes the importance of transparency and communication with consumers, as well as collaboration with regulatory bodies to ensure compliance with safety standards.
The Importance of Continuous Improvement
Continuous improvement is crucial in preventing future recalls and enhancing product safety. Manufacturers must regularly review and update their processes and practices to align with evolving safety standards and consumer expectations. This involves investing in technology, training, and research to stay ahead of potential risks and challenges.
By embracing a culture of continuous improvement, manufacturers can not only enhance product safety but also build consumer trust and loyalty. This proactive approach demonstrates a commitment to quality and safety, which is essential in today’s competitive market.
Consumer Awareness and Education
Consumer awareness and education are critical components in preventing and managing food recalls. By equipping consumers with the knowledge and tools needed to make informed choices, they can better protect themselves and their families from potential health risks.
Educational campaigns and resources can help consumers understand the risks associated with certain products and how to identify recalled items. This includes information on reading labels, understanding expiration dates, and recognizing signs of contamination or spoilage.
Empowering Consumers Through Information
Empowering consumers through information is key to enhancing awareness and education. This involves providing clear and accessible information about recalls, safety standards, and best practices for food handling and storage. By making this information readily available, consumers can make better choices and reduce the risk of exposure to harmful products.
Social media and digital platforms play a significant role in disseminating information and engaging with consumers. By leveraging these channels, manufacturers and regulatory bodies can reach a wider audience and promote awareness and education on food safety.
Role of Regulatory Bodies
Regulatory bodies play a crucial role in ensuring food safety and managing recalls. These organizations establish and enforce safety standards, conduct inspections and audits, and oversee the recall process. Their primary goal is to protect public health and ensure that food products are safe for consumption.
Regulatory bodies work closely with manufacturers to investigate issues, identify the root cause of recalls, and implement corrective actions. They also provide guidance and support to manufacturers in complying with safety standards and regulations.
Collaboration and Compliance
Collaboration and compliance are essential in ensuring the effectiveness of regulatory bodies in managing recalls. Manufacturers must work closely with these organizations to ensure transparency and accountability in the recall process. This involves providing accurate and timely information, cooperating with investigations, and implementing corrective measures as required.
By fostering a collaborative relationship with regulatory bodies, manufacturers can enhance their compliance with safety standards and reduce the risk of future recalls. This partnership is crucial in maintaining consumer trust and ensuring the overall safety of food products.
Economic Impact of the Recall
The economic impact of the top ramen recall is significant, affecting various stakeholders, including manufacturers, retailers, and consumers. For manufacturers, the recall can result in substantial financial losses due to the cost of removing affected products, conducting investigations, and implementing corrective measures.
Retailers may also experience financial losses as they remove recalled products from their shelves and manage the return or exchange process. Additionally, the recall can impact consumer confidence and brand loyalty, leading to decreased sales and revenue.
Long-Term Implications for the Industry
The long-term implications of the recall for the industry are also noteworthy. Manufacturers may face increased scrutiny and pressure to enhance safety standards and quality control measures. This can lead to increased costs and investments in technology, training, and research.
However, these investments are crucial in preventing future recalls and ensuring the long-term sustainability and success of the industry. By prioritizing safety and quality, manufacturers can build consumer trust and loyalty, ultimately benefiting their brand and bottom line.
Global Perspective on Food Recalls
Food recalls are a global issue, affecting consumers and manufacturers worldwide. The top ramen recall is just one example of the challenges faced by the food industry in ensuring product safety and quality. Different countries have varying regulations and standards for managing recalls, reflecting the diverse landscape of the global food industry.
In some regions, recalls may be more common due to stricter safety standards and better detection methods. In others, recalls may be less frequent but pose significant challenges due to limited resources and infrastructure.
International Collaboration and Harmonization
International collaboration and harmonization are essential in addressing the challenges of food recalls on a global scale. By working together, countries can share best practices, resources, and expertise to enhance food safety standards and improve recall management.
Harmonizing regulations and standards across countries can also facilitate trade and reduce barriers for manufacturers operating in multiple markets. This collaboration is crucial in ensuring the safety and quality of food products worldwide and protecting the health of consumers.
What Are the Future Prospects?
The future prospects for the food industry in the wake of the top ramen recall are promising, with opportunities for innovation and improvement in safety standards and processes. Manufacturers are increasingly investing in technology and research to enhance product safety and quality, driving progress and innovation in the industry.
Additionally, there is a growing emphasis on transparency and communication with consumers, as manufacturers strive to rebuild trust and maintain brand loyalty. This involves providing clear and accessible information about recalls, safety standards, and best practices for food handling and storage.
Embracing Technological Advancements
Embracing technological advancements is key to the future success of the food industry. From blockchain for traceability to AI for quality control, technology offers numerous opportunities to enhance safety and efficiency in production processes.
By leveraging these advancements, manufacturers can improve their ability to detect and prevent potential risks, ensuring the safety and quality of their products. This proactive approach is crucial in maintaining consumer trust and meeting the evolving expectations of the market.
Consumer Feedback and Its Significance
Consumer feedback plays a crucial role in shaping the future of the food industry and addressing the challenges of recalls. By listening to consumer concerns and suggestions, manufacturers can gain valuable insights into their products and identify areas for improvement.
Feedback can also help manufacturers understand consumer expectations and preferences, enabling them to develop products that meet the needs and demands of the market. This engagement is crucial in building consumer trust and loyalty, ultimately benefiting the brand and bottom line.
Leveraging Feedback for Continuous Improvement
Leveraging consumer feedback for continuous improvement is essential in enhancing product safety and quality. By incorporating feedback into their processes and practices, manufacturers can address potential issues and implement solutions that align with consumer expectations and standards.
This proactive approach demonstrates a commitment to quality and safety, which is essential in today’s competitive market. By prioritizing consumer feedback, manufacturers can build a reputation as a reliable and trustworthy brand, ultimately benefiting their business and the industry as a whole.
How Does It Affect Brand Loyalty?
The impact of the top ramen recall on brand loyalty is significant, as consumers may lose trust in the brand and question the safety and integrity of its products. Rebuilding brand loyalty after a recall is a challenging but essential task for manufacturers, requiring transparency, accountability, and communication.
By demonstrating a commitment to consumer safety and satisfaction, manufacturers can rebuild trust and loyalty, ultimately benefiting their brand and bottom line. This involves regular updates, public apologies, and assurance of corrective actions, as well as engagement with consumers on social media and other platforms.
Strategies for Rebuilding Brand Loyalty
Strategies for rebuilding brand loyalty after a recall include transparency and communication, consumer engagement, and continuous improvement in safety standards and processes. By prioritizing these strategies, manufacturers can demonstrate their commitment to quality and safety, ultimately rebuilding consumer trust and loyalty.
Additionally, manufacturers can leverage consumer feedback to address potential issues and implement solutions that align with consumer expectations and standards. By prioritizing consumer feedback, manufacturers can build a reputation as a reliable and trustworthy brand, ultimately benefiting their business and the industry as a whole.
Role of Social Media in Recalls
Social media plays a significant role in managing recalls and communicating with consumers. By leveraging social media platforms, manufacturers can reach a wider audience and provide timely and accurate information about recalls and safety standards.
Social media also enables manufacturers to engage with consumers, addressing concerns and inquiries promptly and transparently. This engagement is crucial in rebuilding consumer trust and loyalty, ultimately benefiting the brand and bottom line.
The Power of Social Media
The power of social media in managing recalls lies in its ability to disseminate information quickly and effectively. By utilizing social media platforms, manufacturers can provide real-time updates and engage with consumers, fostering trust and transparency.
This proactive approach demonstrates a commitment to consumer safety and satisfaction, ultimately rebuilding brand loyalty and trust. By leveraging the power of social media, manufacturers can enhance their communication and engagement with consumers, ultimately benefiting their business and the industry as a whole.
Conclusion
The top ramen recall serves as a reminder of the importance of vigilance and awareness in the food industry. By understanding the causes and implications of recalls, consumers can make informed choices and protect their health. For manufacturers, the recall highlights the need for continuous improvement in safety standards and processes, as well as transparency and communication with consumers.
Through collaboration with regulatory bodies, investment in technology, and engagement with consumers, manufacturers can enhance product safety and quality, ultimately benefiting their brand and the industry as a whole. By prioritizing safety and quality, manufacturers can build consumer trust and loyalty, ultimately benefiting their business and the industry as a whole.
FAQs
- What led to the top ramen recall?
- How did the manufacturer address the recall?
- What should consumers do if they have affected products?
- How can consumers stay informed about recalls?
- What role do regulatory bodies play in managing recalls?
- How can manufacturers prevent future recalls?
The top ramen recall was initiated due to potential health risks associated with certain batches, such as contamination or mislabeling.
The manufacturer responded by halting production, issuing public statements, and collaborating with regulatory bodies to ensure safety.
Consumers should follow the instructions provided by the manufacturer, which may involve returning the products for a refund or exchange.
Consumers can stay informed by following news updates, checking the manufacturer's website, and subscribing to alerts from regulatory bodies.
Regulatory bodies establish safety standards, conduct inspections, and oversee the recall process to ensure public health and safety.
Manufacturers can prevent future recalls by implementing robust quality control measures, investing in technology, and fostering a culture of safety within their organization.
Article Recommendations
- The Shocking Truth About Cheryl Hines Daughters Tragic Accident
- Everything You Need To Know About Irn Bru The Iconic Scottish Soda
- Discover The Latest Movies On The Go With Wwwmovierulzcom

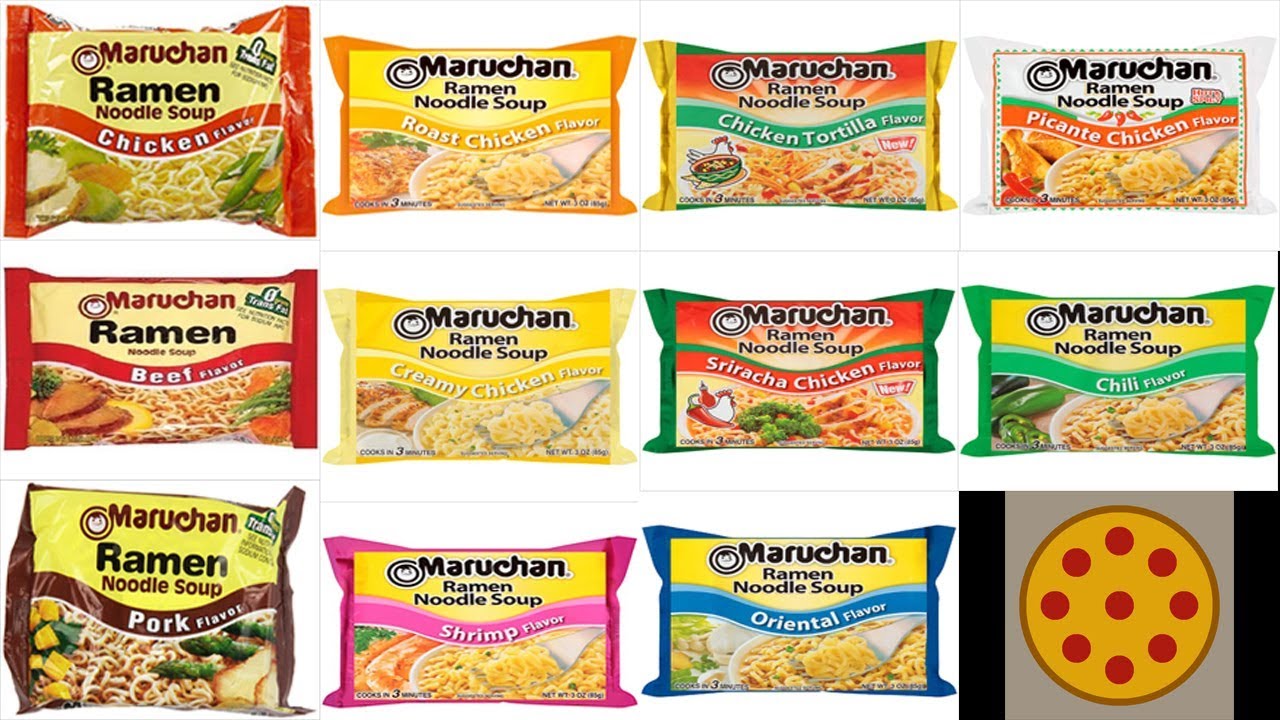